在智能制造的浪潮中,工廠管理者每天要面對海量數據:設備運行參數、生產良率、能耗指標、環境監測值……這些數據分散在PLC、SCADA、MES等不同系統中,如同被鎖在“數據孤島”中的寶藏。物聯網一體屏通過“數據采集-智能處理-視覺呈現”的完整鏈路,正在將抽象的工業數據轉化為直觀的可視化界面,讓管理者在3秒內掌握全局態勢。
一、從“數據報表”到“決策畫布”:可視化展示的進化邏輯
傳統工業數據展示依賴Excel表格或固定報表,存在三大痛點:
- 信息過載:單份報表可能包含50+字段,關鍵指標被淹沒在數據海洋中;
- 響應滯后:人工整理數據耗時2-4小時,決策永遠滯后于生產變化;
- 認知偏差:不同人員對同一組數據的解讀可能完全相反,導致決策分歧。
物聯網一體屏通過三大設計原則重構數據展示方式:
- 信息密度分層:將屏幕劃分為戰略層(KPI看板)、戰術層(產線狀態)、操作層(設備詳情)三級架構,確保管理者在10米外看到核心指標,3米內獲取關聯信息,1米內深入細節。
- 動態優先級排序:采用“熱力圖+異常標注”技術,自動高亮顯示偏離閾值的數據。例如,當設備溫度超過85℃時,對應指標卡從藍色變為紅色并閃爍提醒。
- 多模態交互:集成觸摸、語音、手勢控制,支持管理者通過“滑動切換產線”“語音查詢故障碼”等自然交互方式獲取信息。某汽車工廠項目顯示,這種設計使數據查詢效率提升60%。
二、數據融合引擎:打破“系統壁壘”的關鍵技術
工業現場的數據源高度分散,物聯網一體屏需具備強大的數據融合能力:
- 協議轉換網關:內置支持Modbus、OPC UA、Profinet、MQTT等20+種工業協議的解析模塊,可直連PLC、傳感器、機器人等設備。某電子廠項目通過統一協議轉換,將數據采集周期從15分鐘縮短至3秒。
- 邊緣計算預處理:在一體屏內嵌輕量化AI模型,對原始數據進行清洗、聚合和初步分析。例如,將100臺注塑機的溫度數據實時計算為“產線平均溫度”“溫度標準差”等派生指標,減少云端傳輸壓力。
- 時空數據對齊:解決不同設備采樣頻率不一致的問題。通過時間插值算法,將低頻數據(如每小時采集的能耗值)與高頻數據(如每秒采集的設備狀態)對齊到同一時間軸,確保可視化分析的準確性。
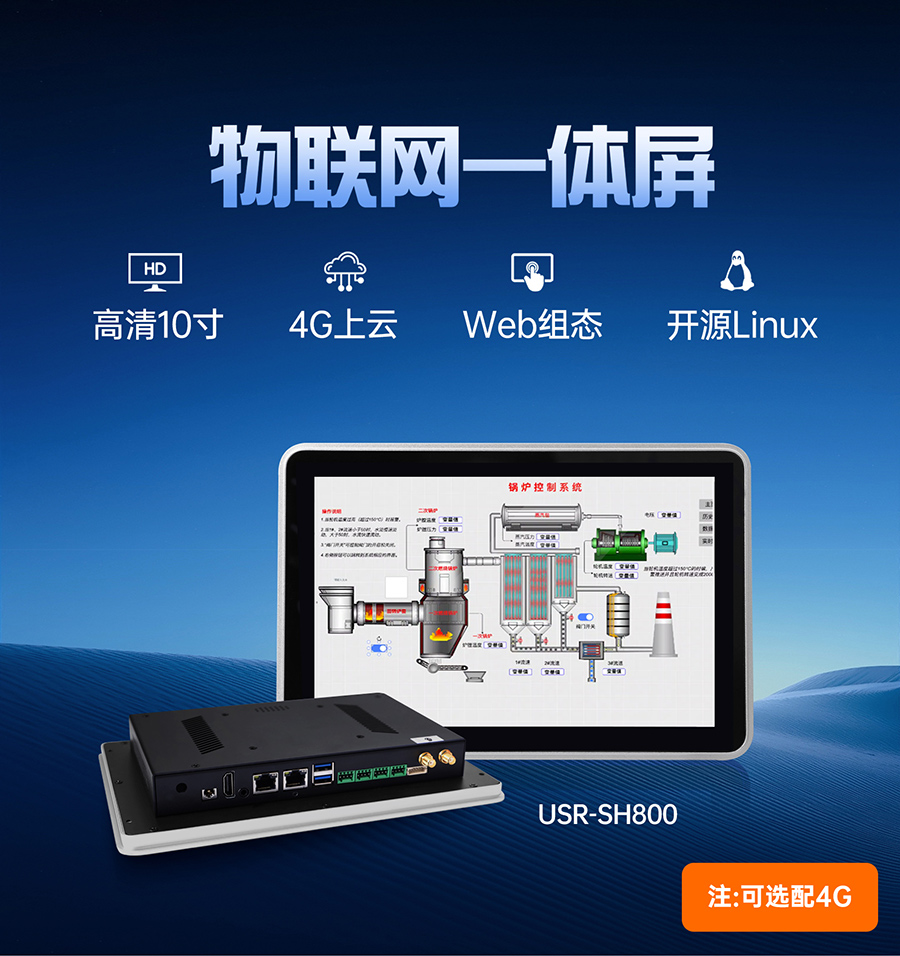
三、可視化設計方法論:讓數據“自己說話”
優秀的可視化界面需遵循“3C原則”:清晰(Clear)、一致(Consistent)、有說服力(Convincing)。具體實踐中需掌握五大技巧:
1. 指標體系構建:從“海量數據”到“關鍵洞察”
采用“金字塔模型”篩選指標:
- 頂層指標:反映企業戰略目標(如OEE、單位能耗成本);
- 中層指標:支撐頂層指標的可分解要素(如設備故障率、換模時間);
- 底層指標:直接采集的原始數據(如電機電流、液壓壓力)。
某光伏企業通過該模型,將監控指標從200+個精簡至18個核心指標,管理者決策效率提升40%。
2. 圖表類型選擇:用“對的圖形”說“對的話”
不同數據關系需匹配不同圖表:
- 趨勢分析:折線圖(適合展示溫度隨時間變化);
- 占比對比:堆疊面積圖(適合展示不同產品線的能耗構成);
- 空間分布:熱力圖(適合展示工廠不同區域的溫濕度差異);
- 異常檢測:箱線圖(適合快速識別設備振動值的離群點)。
3. 動態效果設計:避免“為動而動”的誤區
動態效果應服務于信息傳遞,而非視覺炫技:
- 漸進式加載:數據量較大時,采用“骨架屏+分塊渲染”技術,避免界面卡頓;
- 智能刷新:對變化頻繁的指標(如設備狀態)采用實時刷新,對穩定性指標(如產線良率)采用按需刷新;
- 過渡動畫:在頁面切換或數據更新時,使用0.3秒內的淡入淡出效果,減少視覺干擾。
4. 色彩管理系統:用“數據語言”替代“藝術語言”
工業可視化需建立嚴格的色彩規范:
- 狀態編碼:綠色(正常)、黃色(預警)、紅色(故障)、藍色(待機);
- 數據梯度:采用單色系漸變(如藍-淺藍-白)展示連續變量(如壓力值);
- 對比度控制:確保文字與背景的對比度≥4.5:1,滿足無障礙設計標準。
5. 多終端適配:從“大屏中心”到“全場景覆蓋”
物聯網一體屏需支持多種顯示形態:
- 車間看板:采用55-86英寸工業級觸控屏,防水防塵設計,適應-10℃~50℃環境;
- 移動端:通過HTML5技術實現與PC端一致的交互體驗,支持管理者隨時隨地查看數據;
- AR眼鏡:在設備巡檢場景中,通過AR疊加顯示設備實時參數與歷史維修記錄。
四、行業場景化實踐:從“通用模板”到“精準適配”
不同行業對可視化展示的需求存在顯著差異:
1. 流程型制造(如化工、冶金)
重點展示工藝流程的連續性:
- 采用管道圖+數據標簽的方式,實時顯示反應釜溫度、壓力、流量等參數;
- 通過顏色漸變展示工藝段的運行狀態(如綠色=穩定、黃色=波動、紅色=異常);
- 集成DCS系統數據,實現“一鍵停機”等緊急控制功能。
2. 離散型制造(如汽車、3C)
重點展示產線的節拍與效率:
- 使用甘特圖展示訂單進度與設備利用率;
- 通過數字孿生技術,在屏幕中1:1還原物理產線,實時映射設備狀態;
- 集成ANDON系統,快速定位故障點并觸發維修工單。
3. 能源管理(如電力、光伏)
重點展示能源流向與損耗:
- 采用桑基圖展示電能的產生、傳輸、分配與消耗過程;
- 通過三維地圖展示分布式能源站的位置與運行狀態;
- 集成氣象數據,預測光伏發電量并優化儲能策略。
五、未來趨勢:從“數據展示”到“智能決策”
隨著AI技術的融入,物聯網一體屏正在向三個方向演進:
1. 預測性可視化
通過LSTM神經網絡預測設備故障概率,在界面中提前顯示“未來24小時風險熱力圖”。某風電場項目通過該功能,將計劃外停機時間減少65%。
2. 根因分析輔助
當指標異常時,系統自動關聯歷史數據與知識庫,推薦可能的故障原因。例如,當注塑機廢品率上升時,屏幕彈出提示:“建議檢查:1.料筒溫度;2.模具冷卻水流量;3.機械手抓取位置”。
3. 自然語言交互
集成NLP技術,支持管理者用自然語言查詢數據。例如,輸入“查看上周三下午3點,2號產線的能耗最高的設備”,系統自動生成對應圖表。
讓數據成為“會說話的生產力”
物聯網一體屏的實時數據可視化展示,本質是重構“人-數據-機器”的交互方式。當管理者無需在多個系統間切換即可獲取全局視角,當異常數據能主動“跳”到眼前而非被動查找,當歷史經驗能通過可視化模板快速復用,我們正見證一場靜默的革命:工業物聯網技術正在將“沉睡的數據”轉化為“可執行的洞察”,為精益生產提供決策支撐。對于從業者而言,把握這一趨勢需關注三個維度:深入理解行業工藝流程、掌握數據融合與可視化設計技術、構建開放兼容的生態系統。在未來的智能工廠中,每一塊屏幕都將成為連接物理世界與數字世界的“決策窗口”,共同推動制造業向更高效率、更低成本、更可持續的方向演進。