在傳統工業場景中,設備巡檢需要工程師手持記錄本穿梭于嘈雜的車間,參數調整依賴現場操作終端,突發故障往往因響應滯后演變為生產事故。物聯網一體屏通過集成遠程控制與管理功能,正在重構工業設備的運維模式——工程師坐在辦公室的電腦前,就能完成千里之外產線的啟停、參數校準與故障診斷,如同為工業設備裝上了“數字神經末梢”。
一、遠程控制的底層邏輯:從“物理操作”到“數字指令”的跨越
工業設備的遠程控制并非簡單的“遠程開關”,其核心在于構建安全可靠的“指令-執行”閉環。這一過程涉及三大技術突破:
1. 雙向通信協議的“翻譯官”
工業現場存在Modbus、OPC UA、Profinet、CANopen等數十種通信協議,物聯網一體屏需內置協議轉換引擎,實現不同設備語言的“互譯”。例如,某汽車零部件廠商通過一體屏的協議轉換功能,將30臺老式注塑機(使用Modbus RTU協議)與新建的智能產線(使用OPC UA協議)無縫對接,避免了設備改造的高昂成本。
2. 低延遲控制信道的“高速公路”
遠程控制對實時性要求嚴苛:機械臂運動控制需毫秒級響應,溫度調節需秒級反饋。一體屏采用三大技術保障通信質量:
- 5G/Wi-Fi 6雙鏈路冗余:主鏈路故障時自動切換至備用鏈路,確??刂浦噶?丟失;
- QoS流量調度:為控制指令分配最高優先級,避免視頻監控等大流量數據占用帶寬;
- 邊緣計算預處理:在靠近設備的邊緣節點完成部分計算,減少云端往返延遲。某半導體工廠實測顯示,通過邊緣計算將光刻機控制指令的往返延遲從200ms壓縮至35ms。
3. 安全防護體系的“數字堡壘”
遠程控制面臨網絡攻擊、數據泄露等風險,一體屏需構建多層安全防護:
- 設備身份認證:采用X.509數字證書與PKI體系,確保只有授權設備可接入網絡;
- 數據加密傳輸:使用AES-256算法對控制指令與設備狀態進行端到端加密;
- 操作審計追蹤:記錄所有遠程操作的時間、用戶、指令內容,滿足ISO 27001等合規要求。某能源企業項目通過安全審計功能,成功追溯到一起因誤操作導致的設備停機事故。
二、遠程管理的核心場景:從“被動響應”到“主動預防”的升級
物聯網一體屏的遠程管理功能已滲透至工業運維的全生命周期,形成四大典型應用場景:
1. 設備群組的“集中司令部”
在大型工廠中,同一類設備可能分散于不同車間甚至異地工廠。一體屏通過設備分組管理功能,實現:
- 批量參數下發:同時調整100臺CNC機床的加工轉速,誤差控制在±1rpm以內;
- 策略統一配置:為不同產線的空調系統設置相同的溫濕度控制邏輯,避免人為配置差異;
- 能耗對標分析:自動生成設備群組的能耗排行榜,快速定位高耗能異常個體。某鋼鐵企業通過該功能,將高爐風機的能耗標準差從8%降低至2%。
2. 故障預警的“數字哨兵”
結合設備歷史數據與AI算法,一體屏可實現遠程故障預測:
- 振動頻譜分析:通過內置的加速度傳感器采集電機振動數據,識別軸承磨損、齒輪嚙合異常等早期故障;
- 溫度趨勢預測:基于LSTM神經網絡預測設備溫度變化,在達到閾值前2小時發出預警;
- 知識庫關聯推薦:當故障代碼觸發時,自動推薦相似案例的解決方案與維修視頻。某風電運營商項目顯示,該功能使齒輪箱故障的發現時間提前72小時,維修成本降低40%。
3. 遠程協作的“虛擬工作站”
當現場工程師遇到復雜問題時,一體屏可啟動遠程協作模式:
- AR標注指導:專家通過手機/平板攝像頭查看現場畫面,在屏幕上實時標注故障點與操作步驟;
- 多屏共享:支持工程師與專家同時查看設備參數、歷史日志、3D模型等多維度信息;
- 操作權限移交:專家可臨時接管設備控制權,直接完成參數校準或模式切換。某醫療器械廠商通過該功能,將設備調試周期從3天縮短至8小時,專家差旅成本減少90%。
4. 固件升級的“空中加油站”
傳統設備固件升級需停機、插U盤、手動操作,存在數據丟失風險。一體屏支持:
- 差分升級技術:僅傳輸新舊固件的差異部分,將升級包大小壓縮80%以上;
- 斷點續傳:網絡中斷后自動從斷點繼續升級,避免重復下載;
- 回滾機制:升級失敗時自動恢復至舊版本,確保設備可用性。某物流自動化項目通過該功能,在2小時內完成200臺AGV小車的固件升級,期間零故障發生。
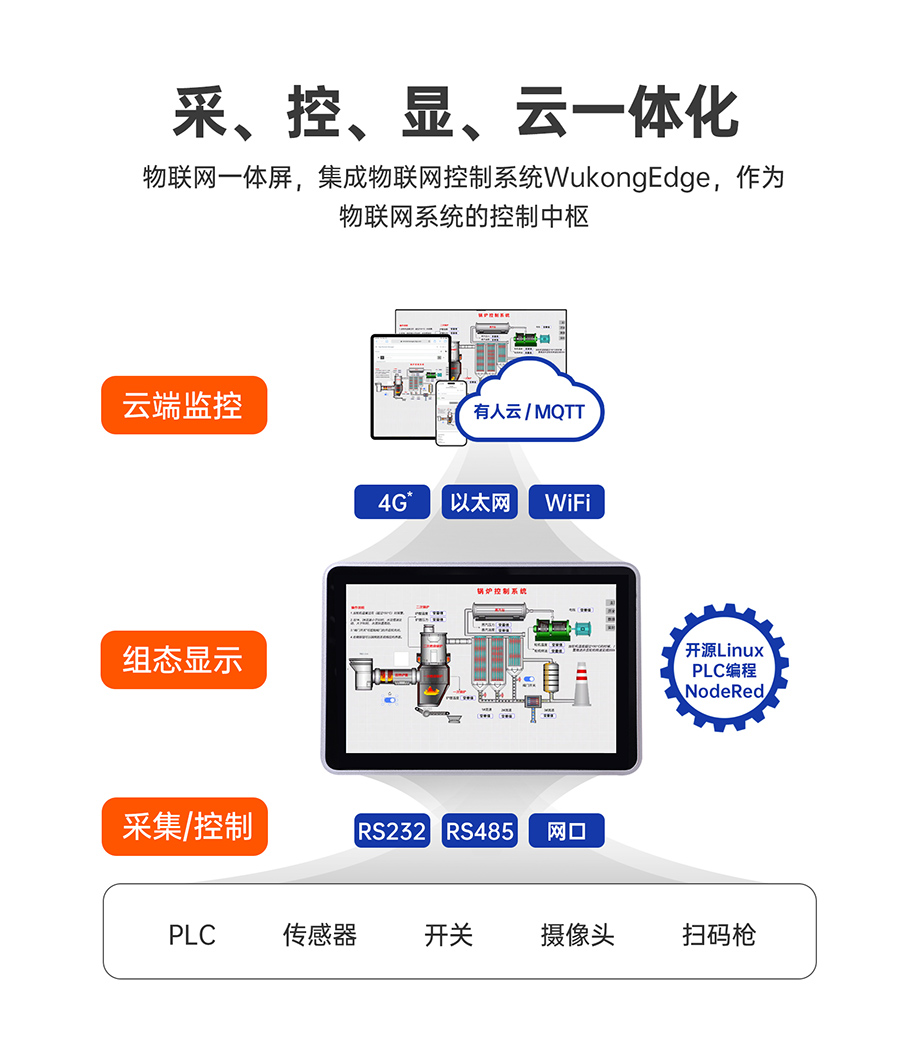
三、行業場景化實踐:從“通用方案”到“精準適配”
不同行業對遠程控制與管理的需求存在顯著差異,一體屏需提供定制化解決方案:
1. 流程工業(如化工、電力)
重點保障連續生產的安全性:
- 聯鎖控制:當反應釜溫度超限時,自動遠程切斷進料閥并啟動冷卻系統;
- 冗余設計:采用雙控制器熱備架構,主控制器故障時備用控制器無縫接管;
- 合規審計:完整記錄所有遠程操作,滿足《安全生產法》等法規要求。
2. 離散制造(如汽車、3C)
重點提升產線的柔性化水平:
- 快速換模:通過遠程參數配置,將產線切換時間從2小時縮短至20分鐘;
- 質量追溯:記錄每臺產品的生產參數與操作人員,實現全生命周期質量追溯;
- 能耗優化:根據訂單需求動態調整設備運行功率,降低空轉能耗。
3. 基礎設施(如水利、交通)
重點強化無人值守能力:
- 自適應控制:根據水位/車流量自動調整泵站/信號燈的運行策略;
- 災害預警:集成氣象數據,在暴雨/臺風來臨前遠程關閉閥門或啟動應急模式;
- 遠程巡檢:通過攝像頭+AI算法自動識別設備外觀缺陷,減少人工巡檢頻次。
四、技術演進方向:從“遠程操控”到“自主決策”
隨著AI與數字孿生技術的融合,物聯網一體屏的遠程功能正在向三個維度升級:
1. 自主優化控制
通過強化學習算法,一體屏可自動調整控制參數以優化生產指標。例如,某水泥廠項目通過該技術,在保持產品質量穩定的前提下,將窯爐能耗降低6%。
2. 數字孿生映射
在虛擬空間中構建設備的數字孿生體,實現:
- 虛擬調試:在新設備投產前,通過孿生體模擬運行參數,減少現場調試時間;
- 故障復現:在孿生體中重現歷史故障,輔助分析根本原因;
- 預測性維護:結合物理模型與數據驅動模型,更精準地預測設備壽命。
3. 自然語言交互
集成NLP技術,支持工程師用自然語言下達控制指令。例如,輸入“將2號軋機的張力提高5%”或“查找過去一個月內溫度超過90℃的設備”,系統自動解析并執行。
重構工業運維的空間邊界
物聯網一體屏的遠程控制與管理功能,本質是打破物理空間對工業運維的限制。當工程師無需親臨現場即可完成設備啟停、參數調整與故障診斷,當千里之外的產線能根據市場需求動態調整生產策略,當歷史經驗通過數字孿生快速復用于新設備調試,我們正見證一場靜默的革命:工業物聯網技術正在將“空間距離”轉化為“數據鏈路”,為精益生產提供更高效、更安全、更靈活的運維范式。對于從業者而言,把握這一趨勢需關注三個維度:深入理解行業工藝流程、掌握低延遲通信與安全防護技術、構建開放兼容的生態系統。在未來的智能工廠中,每一塊一體屏都將成為連接物理設備與數字世界的“控制中樞”,共同推動制造業向更高自動化、智能化水平演進。